In the modern production of plastic products, the overmolding process is playing an increasingly important role. With its unique technical characteristics and wide application range, it endows many products with superior performance and appearance. This article explores the mysteries of the overmolding process.
Overmolding is a special injection molding technique. It involves placing a pre-formed part (usually called an insert) into an injection mold first, then injecting another plastic material into the mold cavity so that the newly injected plastic tightly wraps the insert, forming a complete plastic product with a composite structure.
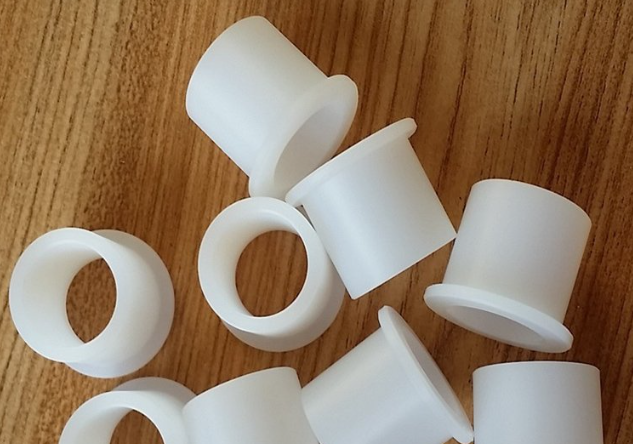
The working principle is based on the thermoplastic property of plastics. Inserts typically have specific shapes and functions before being placed into the mold—for example, metal inserts may provide strength and conductivity, while plastic inserts may achieve specific structural or aesthetic effects. When the high-temperature molten overmolding plastic is injected into the mold cavity, it flows around the insert and cools and solidifies under the constraint of the mold, eventually bonding firmly with the insert. This bonding process relies not only on the mechanical bite force generated by plastic cooling shrinkage but may also involve physical adsorption or chemical bonding between the plastic and the insert surface (in cases of specific material combinations).
Material Selection: Choose suitable insert materials based on the product’s intended use and performance requirements, such as metals (e.g., copper, aluminum, stainless steel for strength, conductivity, or magnetism), engineering plastics (e.g., PC, nylon for structural compatibility), and ceramics.
Forming and Processing: Machine (e.g., turning, milling, stamping) or mold (e.g., injection molding, die casting) the insert material into the required shape and dimensional accuracy. Ensure the insert surface is clean, free of oil and impurities, to facilitate bonding with the overmolding plastic.
Preprocessing: Some inserts may require preprocessing, such as degreasing and surface roughening (e.g., sandblasting) for metal inserts to increase surface roughness and bonding strength, or preheating for certain plastic inserts to reduce temperature differences and internal stress.
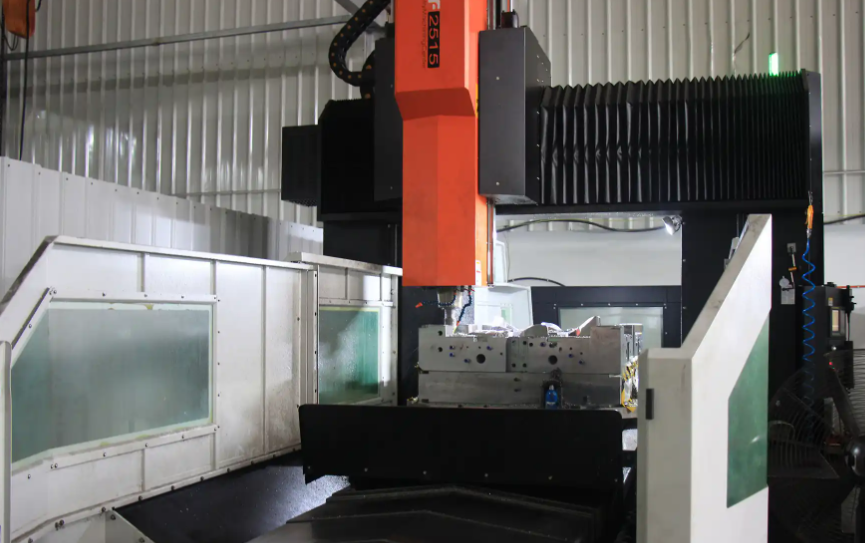
Design Key Points: Overmolding molds are complex and must consider insert placement, positioning accuracy, and plastic melt flow paths. The mold must prevent insert displacement or deformation during injection and provide smooth flow channels for uniform overmolding. Special insert positioning devices (e.g., locating pins, slots) are often designed to ensure accuracy.
Manufacturing and Debugging: Manufacture molds with high-precision equipment per design drawings. After completion, rigorously debug for smooth opening/closing, component fit accuracy, and adjust injection parameters via trial molding to ensure qualified production.
Plastic Material Selection: Choose overmolding plastics compatible with inserts in terms of thermal expansion coefficient and chemical compatibility—e.g., low-shrinkage plastics with strong metal adhesion for metal inserts. Also consider mechanical properties, weather resistance, and appearance.
Parameter Setting: Precisely set injection parameters (pressure, speed, melt temperature, mold temperature, holding pressure/time) based on material properties, mold structure, and product requirements. These parameters critically affect overmolding quality—e.g., proper pressure/speed ensures full cavity filling, while optimal mold temperature controls cooling for dimensional accuracy.
Operation: Place inserts accurately in the mold, close the mold, heat plastic to melt, and inject via screw. Monitor machine status and parameters to ensure process stability.
Demolding and Cleaning: Remove the overmolded product from the mold after cooling, taking care to avoid damage. Clean surface flash and burrs for required appearance.
Quality Inspection: Conduct comprehensive checks, including visual inspection (bubbles, cracks, short shots), dimensional measurement, and performance tests (bond strength, mechanical properties). Only qualified products proceed.
Secondary Processing (if needed): Perform post-treatments like painting, silk-screening, or assembly to enhance appearance and functionality.

Combining inserts with overmolding plastics integrates multiple functions into one product. For example, embedding metal shielding layers in electronic casings achieves lightweight aesthetics and electromagnetic shielding; inserting metal cores in handles enhances strength while soft rubber overmolding improves grip comfort and anti-slip properties.
Mechanical Enhancement: Metal inserts significantly boost strength, hardness, and wear resistance—e.g., metal bushings in plastic gears withstand higher torque, and metal reinforcing ribs in plastic structures enhance impact resistance.
Aesthetic Improvement: Diverse colors and textures of overmolding plastics enable unique appearances, such as two-tone or multi-tone designs in mobile phone casings to enhance market appeal.
Despite complexity, overmolding reduces overall costs by minimizing component count and assembly steps. Additionally, using cost-effective overmolding plastics while reserving high-performance materials for inserts optimizes material usage.
Mobile Devices: Phone casings use metal inserts with plastic overmolding for strength, aesthetics, and signal shielding. Buttons and charging ports often feature rubber overmolding for tactile feedback and water/dust resistance.
Home Appliances: Power tool handles combine metal/hard plastic cores with soft rubber overmolding for comfort and grip. Control panels of refrigerators and washing machines use overmolded buttons and trims for durability and aesthetics.
Interior Parts: Car steering wheels employ metal skeletons with rubber/soft plastic overmolding for strength and comfort. Adjustment buttons and shift knobs use overmolding for improved appearance and usability.
Exterior Parts: Bumpers with plastic bases and elastic rubber overmolding absorb minor impacts, while rearview mirror housings use overmolding for color/texture matching.
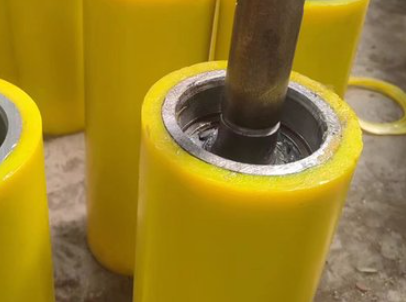
Handheld Equipment: Blood pressure monitors and glucometers use overmolded casings and buttons for ergonomic grip and easy cleaning, meeting hygiene standards.
Medical Catheters: Some catheters feature rigid inner tubes with soft, biocompatible overmolding to ensure flexibility and reduce tissue irritation.
Sports Equipment: Bike handles and racket grips use rubber/silicone overmolding on metal/hard plastic shafts for stability, comfort, and vibration reduction.
Kitchenware: Pan and spoon handles with overmolded insulation and anti-slip layers enhance usability and safety.
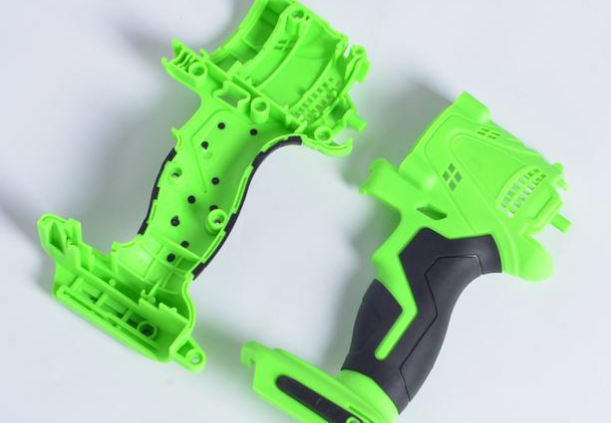
As an advanced plastic molding technology, overmolding demonstrates significant advantages and broad application prospects across industries through its unique principles and processes. By combining the properties of different materials, it not only endows products with enhanced functions and performance but also unlocks greater innovation in design and manufacturing. With advancements in materials science and injection technology, overmolding is poised to play an even more critical role in driving product upgrades and innovation across sectors.
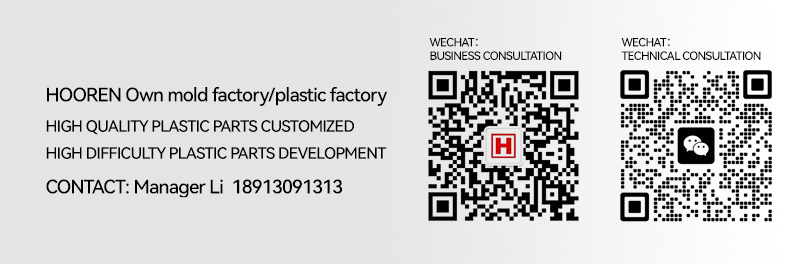