TPV materials, namely Thermoplastic Vulcanizates, are high-performance polymer materials with unique properties and wide application fields.
TPV is a two-phase system composed of a rubber phase and a plastic phase. It typically uses rubber such as ethylene propylene diene monomer (EPDM) as the dispersed phase and thermoplastic plastics such as polypropylene (PP) as the continuous phase. Through dynamic vulcanization technology, the rubber phase forms a fine cross-linked structure within the plastic phase, thus combining the characteristics of both rubber and plastics.
Good Elasticity and Flexibility:
TPV exhibits rubber-like elasticity, maintaining excellent elastic recovery performance within a large deformation range. Meanwhile, it has a certain degree of flexibility, making it suitable for various application scenarios requiring bending or twisting.
Excellent Weather Resistance:
It has good resistance to ultraviolet rays, ozone, oxidation, etc., and can maintain stable performance after long-term outdoor use without easy aging, cracking, or hardening.
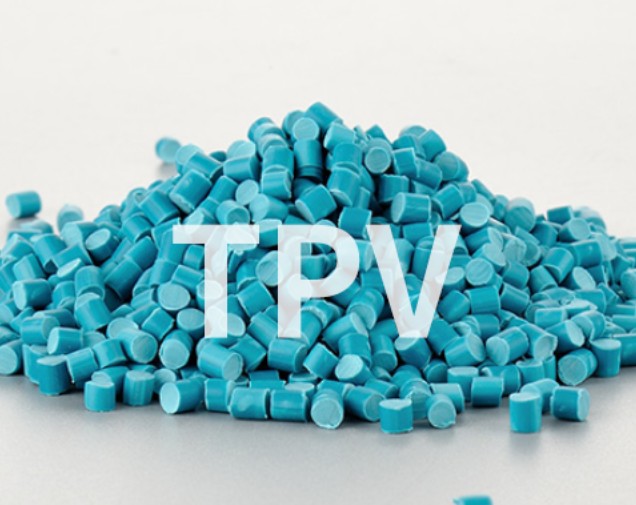
Chemical Corrosion Resistance:
Capable of withstanding the erosion of various chemical substances such as acids, alkalis, and oils, it shows good tolerance in different chemical environments and can be used in scenarios involving contact with various chemical media.
Good Processing Performance:
Compared with traditional rubber, TPV can be processed using thermoplastic processing methods such as injection molding, extrusion, and blow molding. It features high processing efficiency, short molding cycles, and the ability to manufacture complex-shaped products.
Recyclability:
With the recyclable characteristics of thermoplastic plastics, TPV can be reprocessed and reused after disposal, meeting environmental requirements and reducing production costs and environmental impact.
Automotive Industry:
Used to manufacture automotive door and window seals, shock-absorbing components, dust covers, interior parts, etc. Its good weather resistance and oil resistance can adapt to harsh environments such as automotive engine compartments, while its elasticity and flexibility help improve ride comfort and sealing performance.
Electronics and Electrical Appliances:
Applied to insulation sheaths of wires and cables, seals of electronic devices, buttons, etc. TPV’s aging resistance and good electrical insulation performance ensure the safety and reliability of electronic products during long-term use.
Construction Industry:
Can be used for building door and window sealing strips, waterproof membranes, building expansion joint sealing materials, etc. Its excellent weather resistance and water resistance enable it to long-term play a sealing and waterproof role in the construction field, improving the sealing and waterproof performance of buildings.
Medical Devices:
Due to TPV’s good biocompatibility and chemical resistance, it is used to manufacture seals, catheters, medical tubing, and other medical devices, meeting the requirements for material safety and performance stability in medical equipment.
Other Fields:
Also widely used in sports equipment, daily necessities, footwear, etc. For example, handle covers in sports equipment, shoe soles, and side strips in sports shoes leverage TPV’s elasticity and comfort to improve product performance and user experience.