Definition: Specialized tools for manufacturing automotive plastic components.
Principles:
Clamping and injection molding: Fixing molds and injecting molten plastic.
Pressure holding and plasticization: Maintaining pressure to ensure material densification.
Mold opening and ejection: Releasing the molded part after cooling.
Movable and fixed molds: Fixed separately during injection molding.
Gating system: Guides plastic melt, divided into hot and cold runner types.
Temperature control system: Water circuits regulate temperature to aid curing.
Ejection mechanism: Includes ejector pins for demolding.
Ventilation system: Grooves on parting surfaces to exhaust air.
Guiding mechanism: Guide pillars ensure mold alignment.
Design: Determine structure based on injection machines and plastic parts.
Manufacturing: Involves machining, assembly, polishing, mold testing, and modification.
Materials: Select high-temperature resistant plastics and mold steels.
Structure: Optimize temperature control, runner/gate design, and reinforce structural rigidity.
Process: Precisely control temperature, pressure, injection speed, and cooling time.
Machining: Apply surface treatment and precision machining techniques.
Quality control and maintenance: Implement online inspection, manage mold lifecycle, and promote eco-friendly recycling.
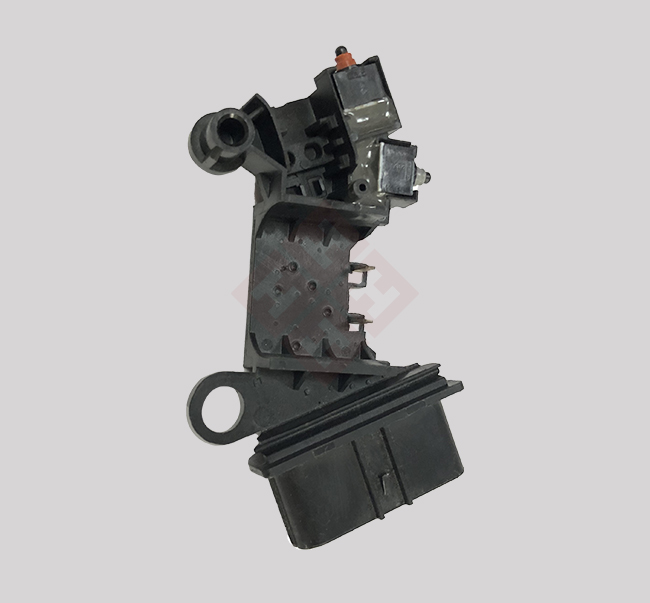
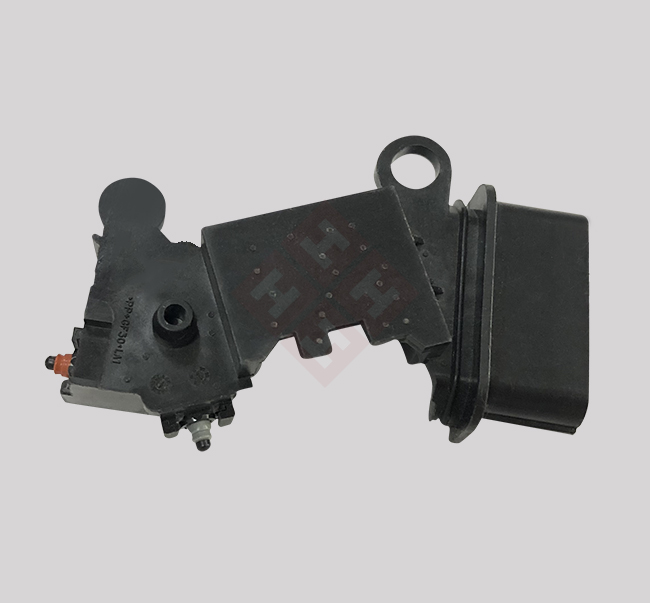